Selecting the appropriate crusher for an aggregate plant is a crucial process to ensure the success of the operation. From technical specifications to production needs, various factors must be analyzed to make the best decision. This article explains the aspects to consider when choosing a crusher and how to make the optimal choice.
What Is an Impact Crusher?
An impact crusher, also known as an impact mill, is a machine designed to reduce the size of large materials such as stones, minerals, and other construction materials. Its operation is based on impact: stones are propelled against impact plates, where they break into smaller sizes. This type of crusher is ideal for producing fine and uniform material.
Technical Specifications of an Impact Crusher
- Production Capacity: From 40 TPH to 350 TPH.
- Feeding Size: Maximum 550 mm.
- Output Size: 0-50 mm.
- Main Applications: Recycling construction materials (concrete, asphalt) and producing aggregates with controlled shapes.
Advantages of an Impact Crusher
- Uniform material production: Ideal for applications requiring a consistent and well-defined size.
- Versatility: Capable of handling a wide range of materials, from hard rocks to recycled materials.
- High efficiency: Designed to maximize production in primary (ICR-P Geminis), secondary (ICR-S Tauro and ICR-S Libra), and tertiary (ICR-T Piscis) applications.
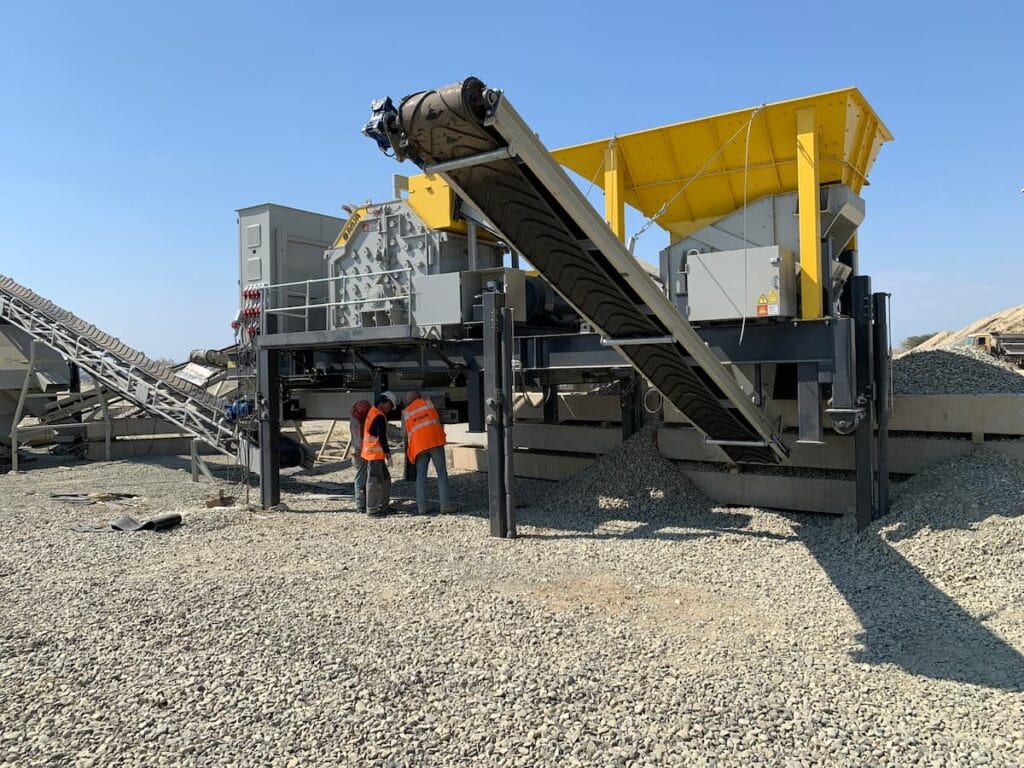
What Is a Jaw Crusher?
Jaw crushers, also known as jaw breakers, are equipment that use a compression mechanism to crush materials. The compression action occurs between two jaws: one fixed and one movable, which moves back and forth to break down the material.
Technical Specifications of a Jaw Crusher
- Production Capacity: From 50 TPH to 950 TPH.
- Maximum Feeding Size: 1,000 mm.
- Output Size: 0-200 mm.
- Main Applications: Industries such as mining, construction, recycling, and cement production.
Advantages of a Jaw Crusher
- Robustness: Designed to handle extremely hard and abrasive materials like granite, basalt, and porphyry.
- Primary applications (JCR-P Leo): Ideal for initial crushing of large blocks.
- Durability: Its simple design and durable components ensure a long lifespan and easy maintenance.
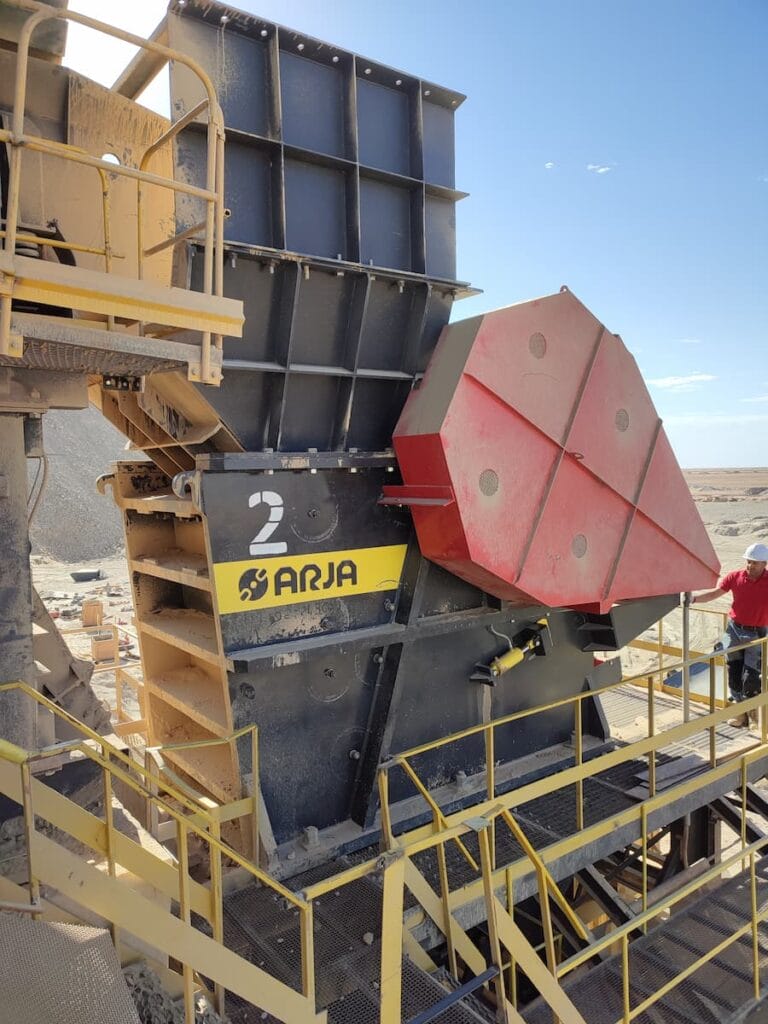
Key Differences Between Impact Crushers and Jaw Crushers
Impact Crushers
- Best suited for secondary and tertiary applications.
- Ideal for producing cubic and uniform material.
- Less efficient with extremely hard and abrasive materials.
Jaw Crushers
- Perfect for primary applications and pre-crushing.
- Excellent for handling large, high-hardness materials.
- Produce less uniform material compared to impact crushers.
When to Use a Combination of Both
Jaw and impact crushers are essential equipment in material crushing processes across various industries. Each offers particular advantages depending on the material type and the process stage in which they are used. While both aim to reduce material size, their designs and operations make them more effective in different contexts. For this reason, many processing plants use these crushers complementarily, as they play specific roles in different stages of the crushing process. This allows plants to maximize both efficiency and the quality of the final material, leveraging the strengths of both machines.

Key Factors for Choosing Between Both Crushers
1. Material Type
- Hard and abrasive materials: Opt for a jaw crusher.
- Recycled or less abrasive materials: The impact crusher is ideal.
2. Desired Production
- For high volumes in the initial stage, use a jaw crusher.
- For quality finishes, complement with an impact crusher.
3. Feeding and Output Sizes
- Jaw crushers handle large material blocks.
- Impact crushers refine material to achieve specific sizes.
4. Costs and Maintenance
- Jaw crushers: Easy maintenance, ideal for demanding applications.
- Impact crushers: Higher initial investment but produce superior quality material.
Choosing the Right Configuration
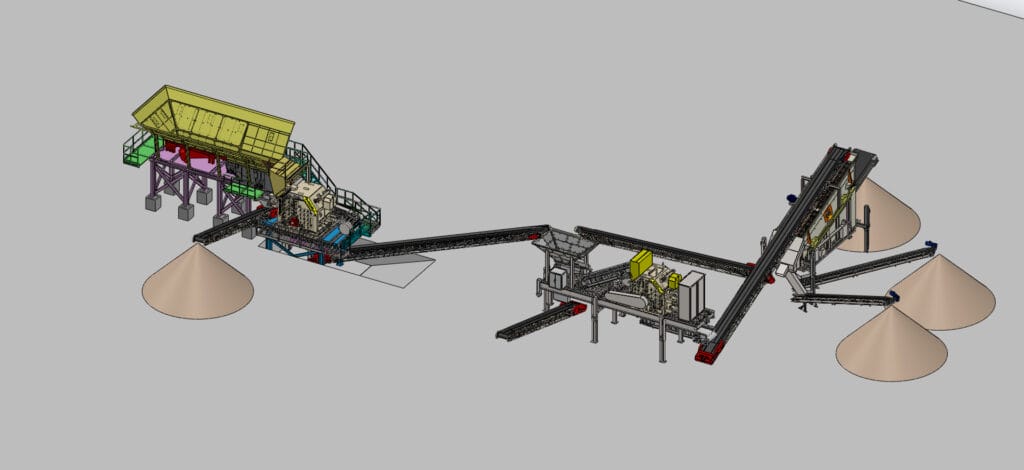
Deciding between an impact crusher, a jaw crusher, or a combination depends on the specific needs of your aggregate plant. Analyzing factors such as material type, desired volumes, and final product size is crucial to making an informed decision.
Recommendation: Consult an expert to assess the needs of your plant and ensure that the chosen configuration maximizes efficiency and meets your production goals.