Impact crusher liners are key elements in ensuring the efficiency and durability of these machines, widely used in the mining and aggregates industry. Designed to withstand wear, abrasion, and extreme impact, these liners are made from materials such as manganese castings, chrome-nickel alloys, and ceramics, each with specific applications. Discover the characteristics and advantages of each option to maximize your equipment’s performance.
Impact Crusher Liners: Types and Characteristics
Manganese Castings in Liners
Composition and Properties:
- Work-hardening by impact: Improves wear resistance with use.
- High toughness and ductility: Absorbs large amounts of energy without fracturing.
- Impact wear resistance: Ideal for handling large and hard materials.
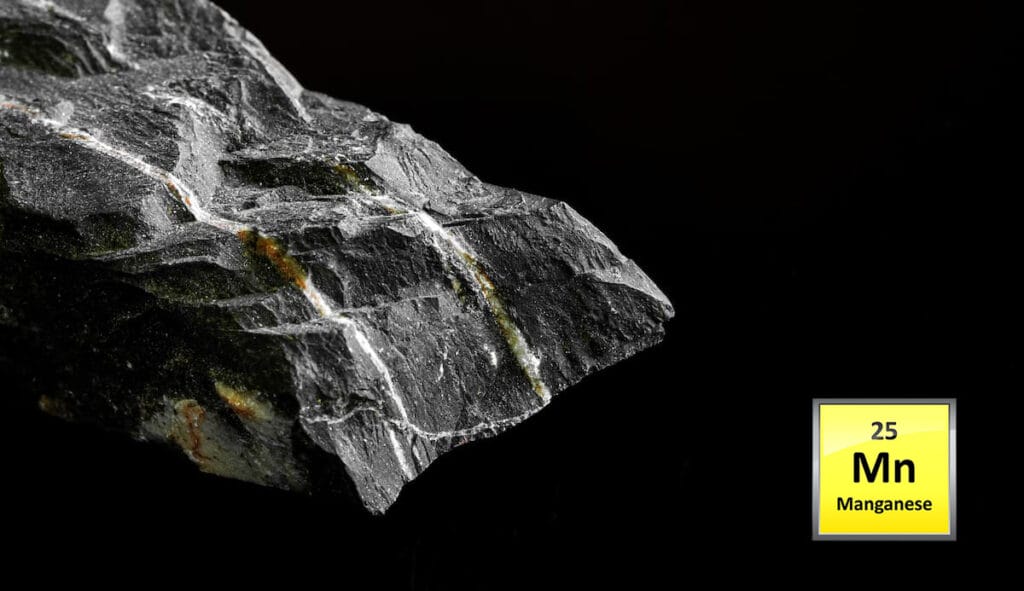
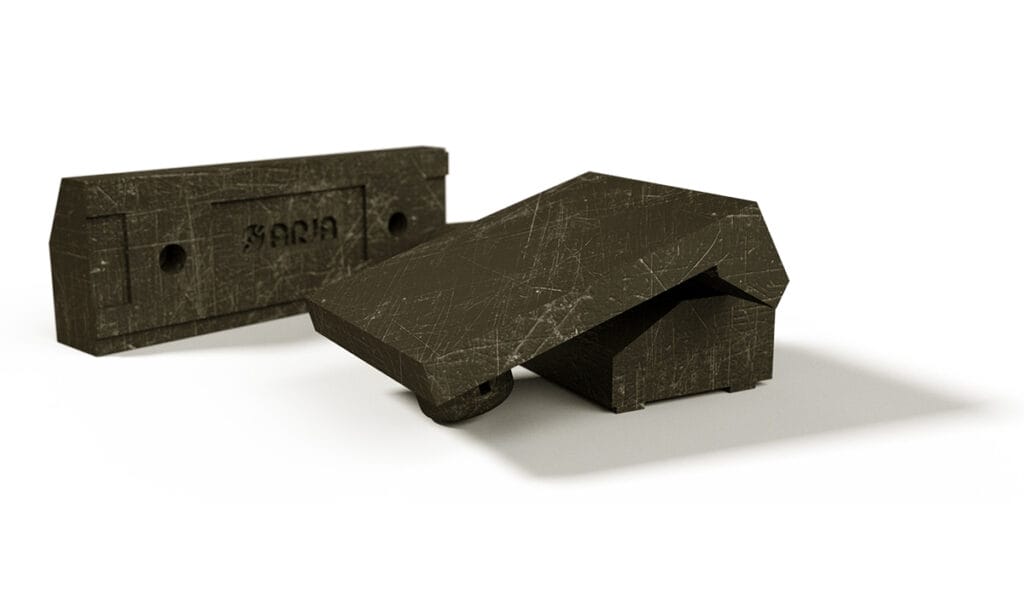
Applications in Impact Crushers:
- Blow bars and impact plates in areas of severe impact.
- Optimal for primary crushing of hard rocks such as granite and basalt.
Advantages and Limitations:
- Advantage: Prolongs lifespan by hardening under continuous impact.
- Limitation: Wears out faster against highly abrasive materials.
Chrome-Nickel Liners: Resistance and Applications
Composition and Properties:
- High resistance to abrasive wear due to hard carbides.
- Improved toughness due to nickel content.
- Thermal and chemical resistance: Ideal for heat and moisture conditions.
Applications in Impact Crushers:
- Liners and blow bars in secondary and tertiary stages.
- Processes combining moderate abrasion and controlled impact.
Advantages and Limitations:
- Advantage: Durable against abrasive materials like quartz and basalt.
- Limitation: Sensitive to extreme impacts and higher production cost.
Ceramic Liners for Extreme Abrasion Zones
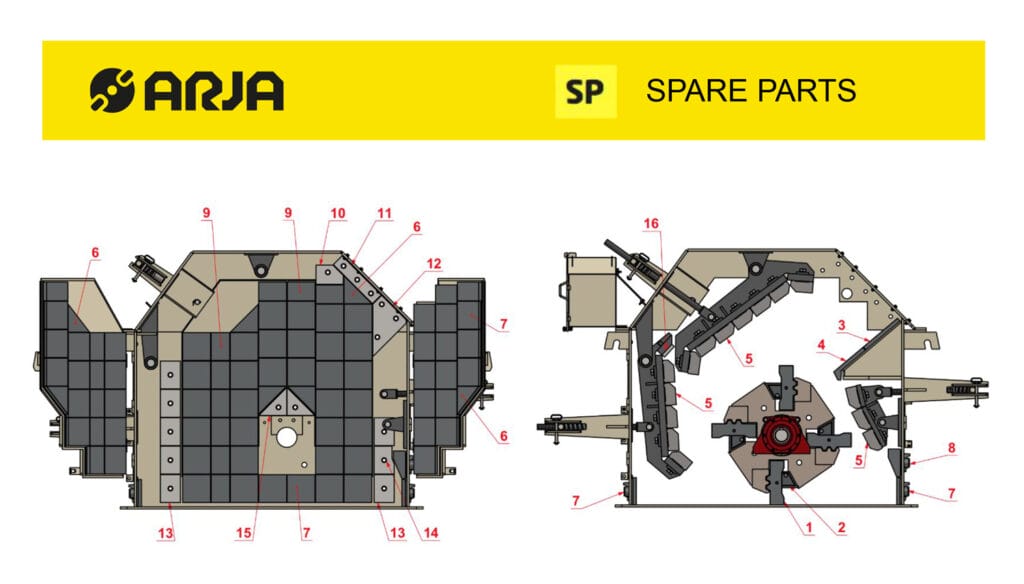
Composition and Properties:
- Made from materials such as aluminum oxides (Al₂O₃) or silicon carbide (SiC).
- Extreme hardness: Better wear resistance than metal alloys.
- Lightweight and thermally resistant.
Applications in Impact Crushers:
- Liners in extreme abrasion zones, such as crushing chambers and discharge points.
- Specific uses in sand crushing, fine minerals, or slag.
Advantages and Limitations:
- Advantage: Exceptional lifespan in abrasive conditions.
- Limitation: Fragile against strong impacts and higher initial cost.
Material Comparison for Impact Crusher Liners
Material | Abrasion Resistance | Impact Resistance | Durability | Typical Applications |
---|---|---|---|---|
Manganese | Medium | High | High | Blow bars, impact plates |
Chrome-Nickel | High | Medium | High | Liners in mixed conditions |
Ceramic | Very high | Low | Very high | Extreme abrasion zones |
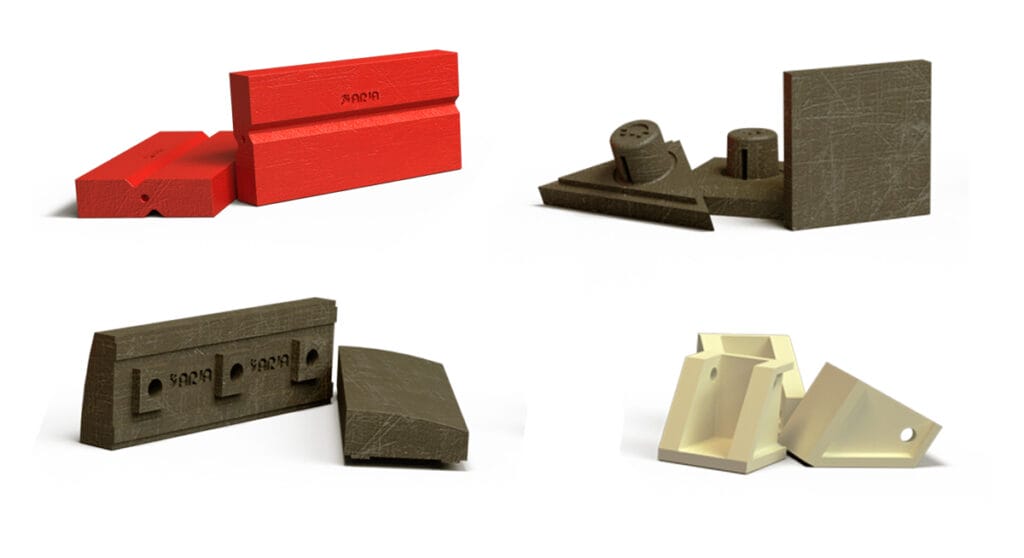
Liner Selection Based on Operation
- Strong and repetitive impact: Manganese castings.
- Moderate abrasion and impact: Chrome-nickel castings.
- Extreme abrasive wear: Ceramic or composite liners.
Key Factors in Using Impact Crushers
Type of Processed Material:
- Hard and abrasive rocks like granite or quartz:
- Primary: Manganese.
- Secondary/Tertiary: Chrome-nickel or ceramic.
- Soft rocks like limestone or gypsum:
- Manganese or economical castings.
Size and Fragmentation of Material:
- In primary stages, where material is large, manganese is preferred.
- In later stages, chrome-nickel and ceramic provide better wear resistance.
Costs and Maintenance:
- High-production quarries invest in premium liners.
- Small and medium quarries opt for manganese, which is more affordable and repairable.
Impact Crusher Liners in Quarries
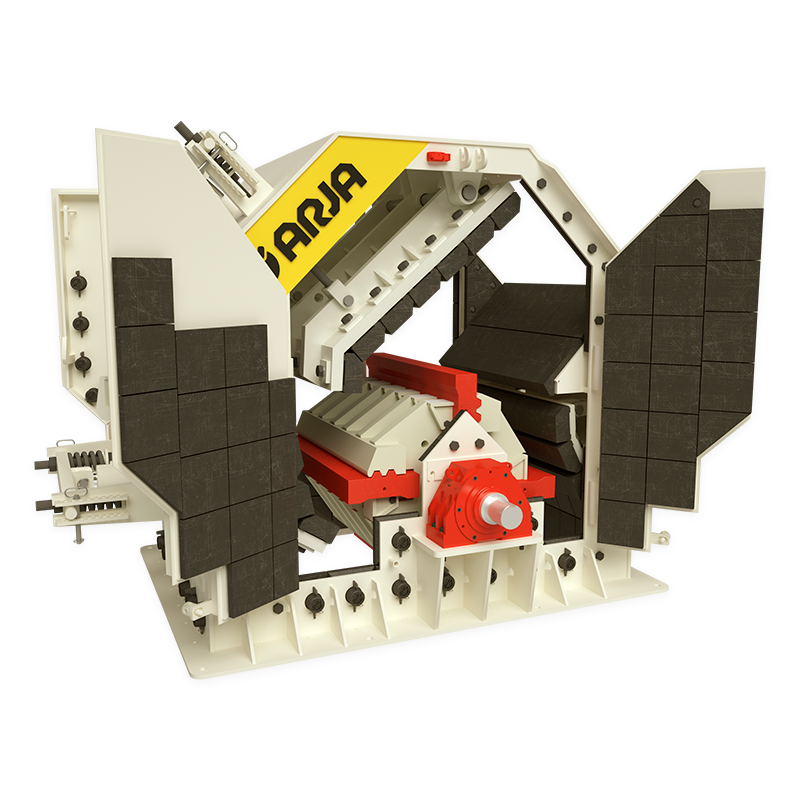
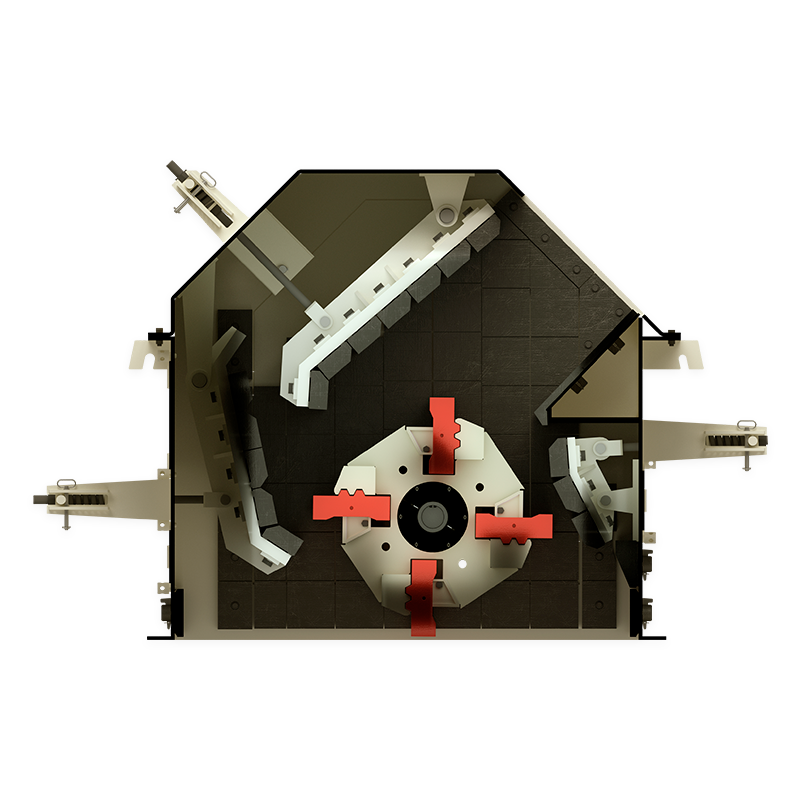
Manganese Castings
Application in Quarries:
- Ideal for primary crushing of hard rocks like granite and basalt.
- Used in blow bars and impact plates.
Advantages:
- Resists heavy rock fragment impacts.
- Progressive hardening with use.
Limitation:
- Wears out quickly against low-impact abrasive materials.
Chrome-Nickel Castings
Application in Quarries:
- Liners in secondary and tertiary stages.
- Finer rock crushing like gravel and crushed sand.
Advantages:
- Excellent abrasion resistance.
Limitation:
- Sensitive to excessive impacts; requires proper pre-processing.
Ceramic Liners
Application in Quarries:
- Specific extreme wear zones such as crushing chambers.
Advantages:
- Exceptional lifespan with abrasive materials.
Limitation:
- Not suitable for strong impacts.
Recommendations and Modern Trends
- Hybrid materials: Combination of ceramic and metal to balance hardness and toughness.
- Automation: Crushers with automatic systems to maximize efficiency.
- Sustainability: Recyclable castings and more energy-efficient processes.